The Versatility of Foam Moulding: Innovations and Applications
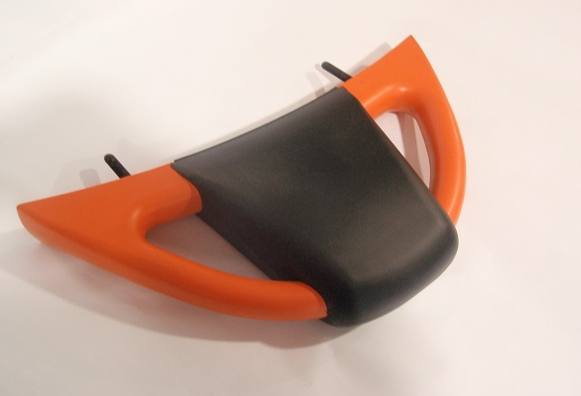
Foam moulding, particularly polyurethane foam moulding, has emerged as a cornerstone technology across various industries, thanks to its unique properties and versatile applications. At Acoustafoam, we specialize in manufacturing polyurethane foam mouldings that are integral to the design and functionality of numerous products. With over 36 years of experience in polyurethane moulding technology, we have honed our skills in bespoke mould design and manufacturing techniques. This expertise allows us to produce high-quality moulded foam products that meet the diverse needs of our clients, ranging from automotive components to furniture fittings.
Polyurethane foam mouldings are often recognized for their durability and adaptability. Integral skin foam, also known as self-skin moulding, combines a soft, flexible core with a tough outer layer that is tear-resistant. This unique structure not only provides protection against scratches and wear but also allows for aesthetic customization, making it ideal for applications such as grab handles, armrests, and decorative trims. The benefits of foam moulding extend beyond its protective qualities; they encompass insulation, soundproofing, and even fire resistance, making it a preferred choice for manufacturers looking to enhance their product offerings.
1. Understanding Polyurethane Foam Mouldings
1.1 What is Polyurethane Foam Moulding?
Polyurethane foam moulding involves a chemical reaction between two components that, when mixed and dispensed into a mould, create a solid structure. This process not only ensures consistency in quality but also enables rapid prototyping and sample production. The resulting products possess a wide range of hardness, measured in Shore A, from 25 to 90, catering to various application needs.
1.2 Key Features of Integral Skin Foam
Integral skin foam mouldings are distinguished by their robust outer skin and micro-cellular foam core. This unique combination allows manufacturers to produce items that are not only comfortable to touch but also capable of withstanding everyday wear and tear. The mould tooling can be customized with different patterns to achieve various textures, such as a leather-like finish, enhancing the aesthetic appeal of the final product.
1.3 Applications of Polyurethane Foam Moulding
Polyurethane foam mouldings find applications in numerous sectors, including:
- Automotive Industry: Used in components such as headrests, armrests, and dashboard trims.
- Furniture Manufacturing: Employed in seating, cushions, and decorative trims.
- Safety Equipment: Integrated into protective gear and safety products.
- Gaming Industry: Utilized in game controllers and equipment for enhanced user comfort.
This versatility highlights the significance of foam moulding in contemporary manufacturing practices.
2. The Foam Moulding Production Process
2.1 Steps Involved in Foam Moulding
The production process of foam moulding encompasses several critical steps:
- Mixing Components: The two parts of the polyurethane mixture are combined, initiating a chemical reaction.
- Dispensing into Moulds: The mixture is dispensed into pre-designed moulds, allowing for specific shapes and structures.
- Curing Process: After a designated time, the material is cured, resulting in a solid product.
- Trimming and Finishing: The cured product undergoes trimming to remove any excess material, ensuring a smooth finish.
These steps ensure that every product adheres to strict quality standards, maximizing durability and functionality.
2.2 Quality Control Measures
Quality control is paramount in foam moulding to ensure that all products meet industry standards. At Acoustafoam, we implement rigorous measures to assess factors such as:
- Density and Hardness: Ensuring consistency in the material properties across batches.
- Tear Strength and Fire Retardant Properties: Testing for durability and safety.
- UV Stability: Ensuring that the products maintain their integrity when exposed to sunlight.
By prioritizing these quality control measures, we can guarantee that our polyurethane foam mouldings consistently exceed customer expectations.
3. Benefits of Using Foam Moulding
3.1 Advantages of Polyurethane Foam Mouldings
The use of foam moulding brings several advantages to manufacturers and end-users alike:
- Durability: Foam mouldings are designed to withstand daily use without compromising their structural integrity.
- Comfort: The soft, flexible nature of the foam ensures comfort in applications such as seating and armrests.
- Aesthetic Flexibility: Manufacturers can customize textures and colors, enhancing the visual appeal of products.
- Insulation Properties: Polyurethane foam provides excellent thermal and sound insulation, making it ideal for construction and automotive applications.
3.2 Environmental Considerations
In recent years, the importance of environmental sustainability has gained prominence in the manufacturing sector. Many foam conversion processes now incorporate eco-friendly materials, minimizing waste and environmental impact. Companies are increasingly looking to develop products that are not only high-quality but also environmentally responsible.
4. Innovations in Foam Conversion Processes
4.1 Advanced Foam Types
Acoustafoam specializes in various types of foam, including:
- Polyurethane Foam: Ideal for cushions and insulation.
- Polystyrene Foam: Lightweight and suitable for packaging and insulation.
- Polyethylene Foam: Durable and moisture-resistant, often used in packaging and padding.
These advanced foam types are essential for meeting the specific needs of different industries, ensuring that manufacturers have the right materials at their disposal.
4.2 Customization Options
Customization is a significant advantage of foam moulding. Clients can specify design, size, and functionality requirements, resulting in tailored solutions that precisely meet their needs. This flexibility is especially beneficial in industries such as automotive and furniture manufacturing, where specific dimensions and functionalities are often critical.
4.3 Environmentally Friendly Innovations
As sustainability becomes a priority, the foam industry is witnessing innovations aimed at reducing environmental impact. This includes using recycled materials in foam production and developing processes that minimize waste. By prioritizing eco-friendly practices, companies like Acoustafoam are contributing to a more sustainable future.
Read Also: PAT Testing Telford: Ensuring Electrical Safety
Conclusion
Foam moulding is an integral technology that underpins many products we use daily, from automotive components to furniture fittings. The versatility of polyurethane foam mouldings, combined with their durability and comfort, makes them an ideal choice for various applications. At Acoustafoam, our commitment to quality, innovation, and environmental sustainability ensures that we provide products that not only meet but exceed industry standards.
As industries continue to evolve, the importance of foam moulding will only grow, driven by technological advancements and changing consumer preferences. Whether you’re looking for custom foam products for automotive applications or furniture design, Acoustafoam is ready to assist you. Contact us today to learn more about how our foam moulding solutions can benefit your business.